In the realm of precise gas analysis, particularly within continuous emissions monitoring systems (CEMS) and process control applications, the integrity of the sample from the point of extraction to the analyser is paramount. A critical, yet often underestimated, component in maintaining this integrity is the heated sample line. Failure to control the sample gas temperature can lead to significant analytical errors, compromising data accuracy and regulatory compliance.
The Peril of Condensation: A Threat to Analytical Accuracy
Gas samples extracted from industrial processes, combustion sources, or environmental atmospheres often contain various components, including water vapor and other condensable species (e.g., certain hydrocarbons, acids like SO₃, or even NOx compounds under specific conditions). The dew point of a gas mixture is the temperature at which water vapor or other condensable components will begin to condense into liquid form at a given pressure. If the temperature of the sample gas drops below its dew point during transport, condensation will inevitably occur.
Consequences of Condensation:
- Loss of Analyte: When condensation occurs, soluble gas components (e.g., SO₂, HCl, NH₃, or even VOCs) can dissolve into the liquid phase. This effectively removes them from the gas stream, leading to artificially low and inaccurate concentration readings at the analyser. This phenomenon is particularly problematic for polar or highly soluble gases.
- Physical Obstruction and Damage: Liquid droplets can accumulate within the sample line, leading to blockages, increased pressure drop, and potential damage to sensitive components of the sampling system or the analyser itself. This can manifest as erratic flow, analyser malfunction, or even complete system shutdown.
- Corrosion: The condensed liquid, especially if it contains acidic components, can be highly corrosive to the sample line materials, leading to degradation, leaks, and contamination of subsequent samples.
- Particulate Accumulation: Condensed moisture can trap and bind particulate matter within the sample line, exacerbating blockages and further compromising sample integrity.
- Delayed Response Times: Liquid accumulation can increase the effective volume of the sample path, leading to longer transport times and delayed response from the analyser, which is unacceptable in dynamic monitoring applications.
The Solution: Maintaining Temperature Integrity with Heated Sample Lines
Heated sample lines are specifically designed to prevent condensation by maintaining the sample gas temperature consistently above its dew point throughout the entire transport path from the sampling probe to the analyser or sample conditioning system. This ensures that all gaseous components remain in their gaseous phase, preserving the original composition of the sample.
Key Principles of Heated Sample Line Operation:
- Constant Temperature Control: Heated lines typically incorporate internal heating elements such as resistance wires or self-regulating heating cables. However, Signal Group distinguishes itself by employing a unique braiding technology that ensures total heat coverage of the entire internal line surface, maintaining a constant and uniform temperature across it all. This advanced design prevents subtle temperature gradients that can occur with other heating methods, offering a significant advantage in sample integrity. Advanced systems often include integrated temperature sensors and controllers to ensure precise temperature regulation, even in fluctuating ambient conditions.
- Dew Point Management: The target temperature for the heated line is determined by the highest expected dew point of the sample gas, typically set with a safety margin (e.g., 10-20°C above the dew point) to account for variations in sample composition or ambient temperature.
- Material Compatibility: The internal tubing of heated lines is constructed from materials (e.g., PTFE, stainless steel) that are chemically inert to the sample gas components and can withstand the elevated temperatures.
- Integrated Components: Many heated sample lines are available as complete bundles, incorporating not only the heated tubing but also electrical lines for power and control, and sometimes even additional tubes for calibration gases or blowback air.
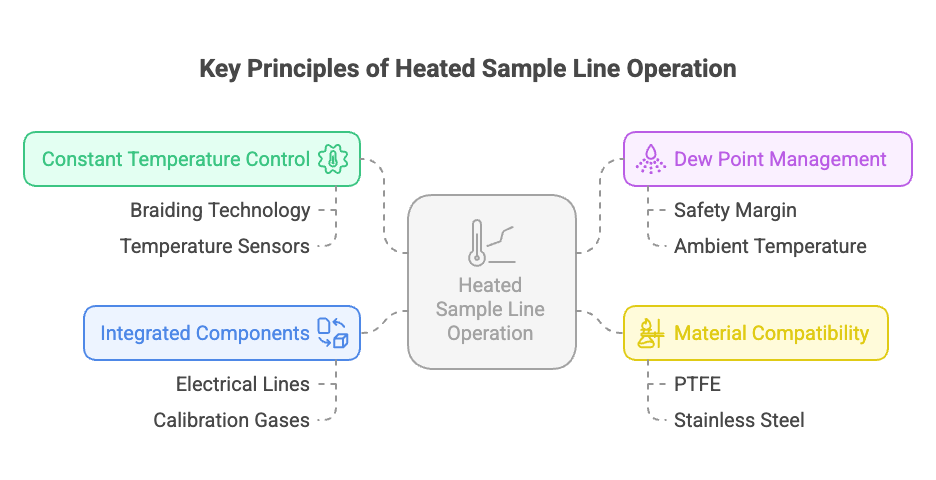
The Significance of the 191°C Standard
The standard temperature of 191°C used for heated gas analysis—especially for sample lines and heated filters—is not arbitrary. It’s carefully chosen based on the physical and chemical properties of certain key analytes, particularly VOCs (Volatile Organic Compounds) and moisture-laden samples. Here’s why:
1. Prevents Condensation of Moisture and VOCs
- Water Vapour: Condenses below ~100°C, depending on the dew point of the gas stream.
- VOCs and Semi-Volatiles: Many VOCs and semi-volatile organic compounds have boiling points between 100°C and 180°C.
A temperature of 191°C is sufficiently high to:
- Prevent water condensation, keeping the sample fully in the gas phase.
- Prevent the adsorption or loss of VOCs to the internal surfaces of sample lines.
- Ensure no phase change occurs that would alter the sample composition before analysis.
2. International Standardisation
US EPA Method 25A, which governs Flame Ionisation Detector (FID) measurements of total hydrocarbons, specifies a minimum sample line temperature of 191°C. This has become a de facto global standard, influencing:
- Continuous Emission Monitoring Systems (CEMS)
- EN 12619, EN 13526, and other European methods
3. Material and Safety Balance
Above 200°C, materials like PTFE, FEP, and other fluoropolymers commonly used in sample lines can begin to degrade or outgas, potentially contaminating the sample. 191°C represents a safe and effective temperature that is:
- Safely below the thermal limits of standard materials.
- Above the boiling point of most interfering or condensable substances.
- Energy-efficient enough for practical and safe long-term use.
Summary of Reasons for the 191°C Standard
Reason | Why 191°C? |
Prevent water condensation | Keeps sample fully in gas phase |
Avoid VOC loss | Above boiling points of most VOCs |
Regulatory compliance | Aligns with EPA and EN methods |
Material constraints | Below degradation point of standard materials |
Industrial standardisation | Widely adopted by analyser manufacturers |
Signal Group’s use of 191°C heated lines (e.g., with the 3010 MiniFID or other VOC monitoring systems) ensures regulatory compliance and preserves sample integrity—especially for low-level hydrocarbon or solvent emissions monitoring.
Signal Group’s Advanced Heated Sample Line Solutions
Signal Group understands that the accuracy of gas analysis begins at the point of sample extraction. Our heated sample line solutions are engineered to provide robust and reliable sample transport, ensuring that the gas presented to the analyser is truly representative of the source.
While specific heated line products are often integrated into our comprehensive sampling systems, the underlying technology and principles are applied across our range of analysers, particularly those designed for challenging applications like continuous emissions monitoring (CEMs) and engine exhaust analysis.
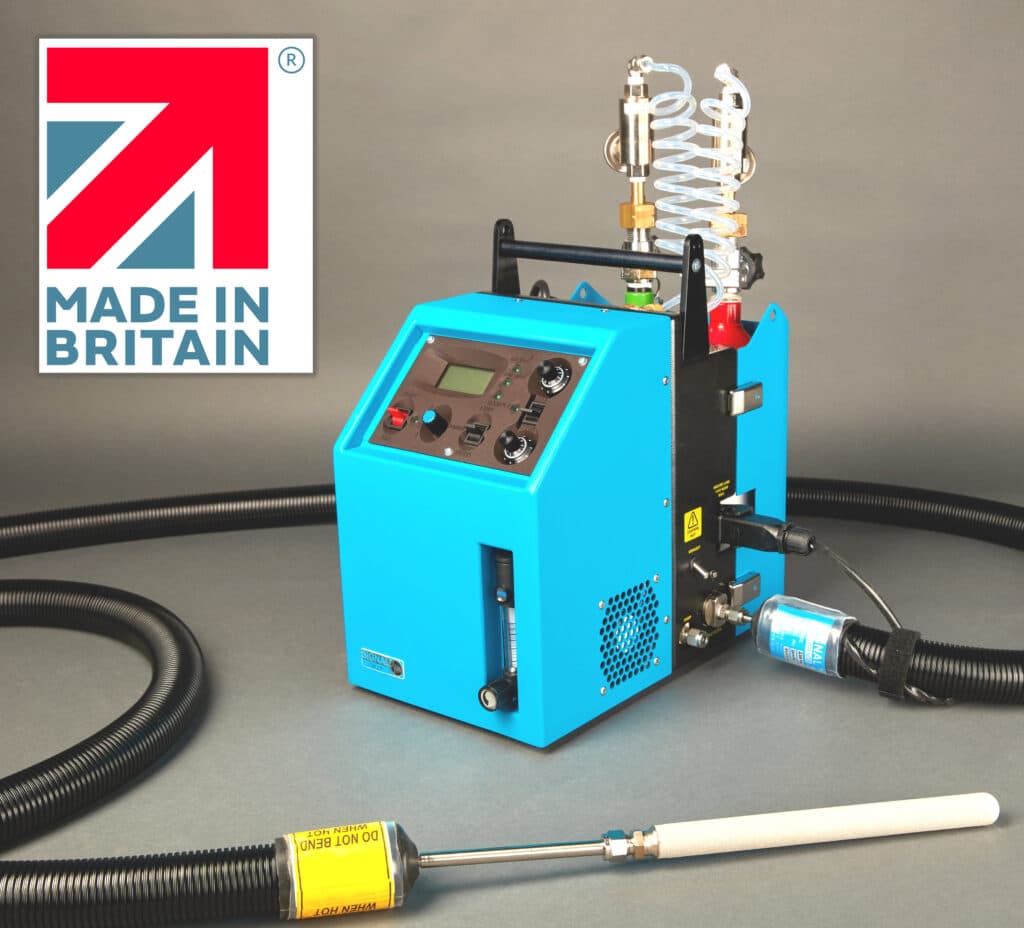
Key Features and Benefits of Signal Group’s Approach to Heated Sample Management:
- Uniform Temperature Distribution with Braiding Technology: Unlike conventional heated lines that may use resistance wires or self-regulating cables, Signal Group’s heated lines leverage a unique braiding technology. This ensures total heat coverage of the entire internal line surface, maintaining a constant and uniform temperature across the entire length. This superior temperature uniformity is critical for preventing localized cold spots and ensuring the complete integrity of the sample, especially for sensitive VOC measurements.
- Preservation of Sample Integrity: By maintaining the sample gas above its dew point, our heated lines prevent the loss of soluble analytes, ensuring that the measured concentrations accurately reflect the source emissions. This is crucial for components like SO₂, NOx, and VOCs, which are highly susceptible to condensation-induced losses.
- Prevention of System Contamination and Damage: The elimination of condensation prevents liquid accumulation, thereby safeguarding the analyser and sample conditioning components from corrosion, blockages, and costly damage. This significantly extends the lifespan of the analytical system and reduces maintenance requirements.
- Rapid Response and Stability: A dry, uncontaminated sample path ensures faster transport times and more stable analyser readings, leading to quicker response to changes in emission levels and improved overall system performance.
- Robust Construction for Demanding Environments: Signal Group’s heated lines are built to withstand harsh industrial environments, offering excellent mechanical durability and thermal insulation. This ensures reliable operation even in challenging outdoor or high-temperature settings.
- Compliance with Regulatory Standards: For applications governed by strict environmental regulations (e.g., EN 14181, US EPA methods), the use of properly designed and maintained heated sample lines is often a mandatory requirement to ensure the validity and representativeness of the monitoring data.
Applications Where Heated Sample Lines Are Indispensable
Heated sample lines are critical in a variety of applications, including:
- Continuous Emissions Monitoring (CEMs): Essential for accurate measurement of pollutants (e.g., SO₂, NOx, VOCs, HCl) from industrial stacks, where flue gases are hot and contain significant moisture.
- Engine and Vehicle Emissions Testing: Crucial for analysing exhaust gases, especially during cold-start conditions or when measuring condensable hydrocarbons and other species.
- Process Gas Analysis: In chemical plants, refineries, and other industrial processes where gas streams contain high dew point components or corrosive gases.
- Environmental Research: For accurate sampling of atmospheric gases or emissions from various sources in research settings.
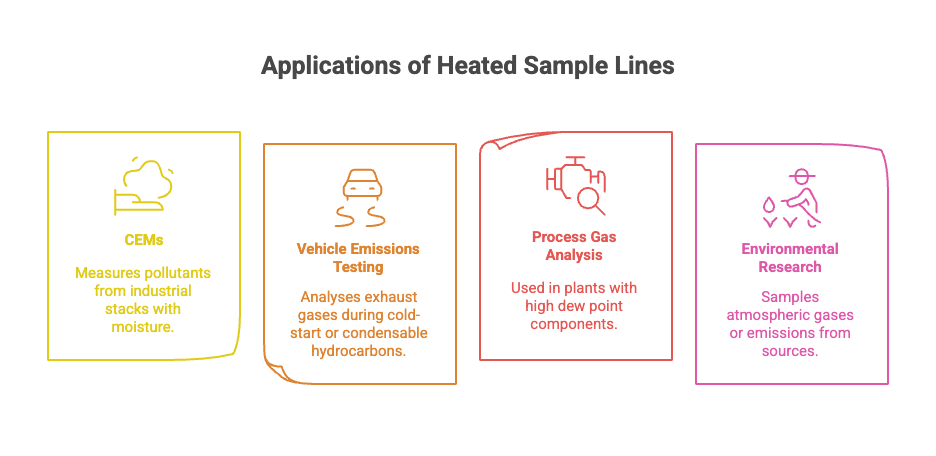
Conclusion: The Foundation of Accurate Gas Analysis
In the complex landscape of gas analysis, the sample line is not merely a conduit; it is an integral part of the measurement system. The judicious application of heated sample line technology is fundamental to overcoming the challenges posed by condensation and ensuring the delivery of a representative, uncompromised gas sample to the analyser. Signal Group’s expertise in designing and implementing these critical components underscores our commitment to providing comprehensive, high-integrity solutions for the most demanding gas analysis applications. By investing in robust heated sample line solutions, industries and researchers can ensure the accuracy, reliability, and regulatory compliance of their analytical data, paving the way for informed decision-making and effective environmental management.
Contact Signal Group for Expert Consultation
To discuss your specific gas analysis requirements and learn more about how Signal Group’s heated sample line solutions can enhance the accuracy and reliability of your measurements, please contact our technical sales team:
Email: sales@signal-group.com Website: www.signal-group.com